Resolving concerns with check valves used at iron works manufacturers
YOKOTA Non-Water Hammer Check Valve (PAT.)
|
Blast furnace
|
First adopted with iron works manufacturers in 1974, the unique mechanism
of the YOKOTA Non-Water Hammer Check Valve has surprised those concerned
with check valves that completely prevent water hammer.
Since then, approximately 1000 of these valves have been used at iron and
steel works manufacturers. You might consider this number insignificant
in view of the numerous valves equipped in these places. However, when
considered in terms of the severe conditions under which the Non-Water
Hammer Check Valve is used, your perspective may change.
With the Non-Water Hammer Check Valve, YOKOTA has provided a solution to
water hammer problems based on consultations with equipment maintenance
supervisors in the iron and steel works industry.
The following are some of the concerns addressed in these consultations.
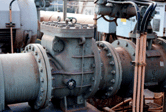
|
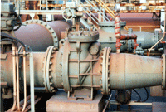 |
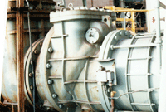
|
The YOKOTA Non-Water Hammer Check Valve, in service at iron and steel works
manufacturers
|
|
The structure of the YOKOTA Non-Water
Hammer Check Valve
|
|
|
(1)
|
Valve arm pin
|
(4)
|
Pin holder
|
(2)
|
Valve disk
|
(5)
|
Valve seat
|
(3)
|
valve cover
|
(6)
|
Hard rubber
for buffering
|
|
|
|
Non-Water Hammer Check Valve SL series
|
|
|
The life expectancy of check valves is, in fact, short. Some of them have
to be replaced any number of times within a year or so because the valve
disk or the valve case becomes worn out due to corrosion, or the valve
arm pin (swing shaft of the valve disk) becomes thin due to wear caused
by sludge.
Are there any valves with longer life expectancy?

|
According to our cause investigations...
|
Industrial water used at iron and steel works manufacturers is repeatedly
used any number of times via recirculation.
In this case, the recirculated water gradually deteriorates causing a rise
in the density of the sludge as it inflows to the check valve, thus, both
wear and corrosion problems occur from the sludge.
Large amounts of seawater are also used by these manufacturers. Large pumps
pump the seawater as a coolant, and the check valve equipped near the pump-discharging
outlet is exposed to the seawater. However, because general check valves
used by these manufacturers are made of cast iron FC, the valve disk and
pin holder have no effective resistance to wear and corrosion.

|
How about the Non-Water Hammer Check Valve?
|
YOKOTA uses stainless steel resistant to both wear and corrosion, which
is produced in-house at our stainless steel casting foundry.
Of course we could produce our product all in stainless steel, but we have
also made a lot of effort on creating products partially made of stainless
steel, for example, just valve arm pins (1 in illustration above), valve
disks (2), and pin holders (4). We have equipped the Non-Water Hammer Check
Valve to the above places where damage has occurred in the past over the
period of a year, and the parts now work fine without needing maintenance
for 5 to 6 years. Moreover, there are many cases where operation has continued
for 10 years without replacing a pin, which causes some maintenance supervisors
to shake their heads in disbelief.
Providing products that meet the customer's budget and usage conditions
is one of the reasons why so much attention has been paid to the Non-Water
Hammer Check Valve.
The problem is that check valves are difficult to disassemble, there are
too many components to be disassembled, and it takes up too much space
when performing the disassembly inspection.
Are there any valves that could make this work more simple?

|
According to our cause investigations...
|
When we look at the comparison table of the check valves below, the general
check valves (counter-weight type, coil spring type, and dashpot type)
are composed of many parts that require a lot of space and time to disassemble.
Judging by the structure alone, it would appear that a lot of time is needed
to remove the bolts and pins to access the inner valve.

|
How about the Non-Water Hammer Check Valve?
|
The structure is very simple. There are no complex components such as counter-weights
or dashpots because the valve case and valve disk are connected only with
a pin.
Therefore, it is extremely rare for the Non-Water Hammer Check Valve to
malfunction, and only a small space is needed for disassembly. Everything
inside the valve can be inspected just by opening the valve cover (3).
When repairing the valve disk (2) with it removed, the valve arm pin and
valve disk can be removed at the same time by removing the two pin holders
(4) located on both the left and right sides because of the pin holder
construction which can be removed in the shaft direction.
This structure has a strong reputation among maintenance supervisors because
it makes maintenance work easier.
Even though new valves are installed, there is leakage from the valve seating
when the valves are completely closed.

|
According to our cause investigations...
|
Since the valves are new, there is no suspicion of valve wear or corrosion.
In this case, the following two causes may be considered.
First, the angle of the valve disk attachment to the valve seat is nearly
0 degrees to vertical, so there is the possibility of less attachment force
depending on the attachment angle of the valve. As a result, the seal between
the valve disk and valve seat may be compromised causing leakage.
Second, pressure due to water hammer has deformed the valve arm pin (swing
shaft of the valve disk), and as a result, the seal between the valve disk
and valve seat may be compromised causing leakage. Iron works manufacturers
are places where the water circulation pipes run all over, so there is
a high possibility of water hammer occurrence caused by water column separation.
In addition, a valve arm pin will be heavily damaged and deformed by just
one occurrence of water hammer.

|
How about the Non-Water Hammer Check Valve?
|
As for the first problem concerning the valve disk and valve seat attachment
angle, the valve seat (5) is constructed at the optimal angle according
to mechanical calculations, and the weight of the valve disk itself is
effectively utilized so that the valve attaches precisely.
As for the second problem, the YOKOTA Non-Water Hammer Check Valve shuts
off water hammer completely, so there is no possibility of deformation
to the valve arm pin.
Sometimes, a "knocking" sound can be heard from inside the valve,
which makes it seem that the valve disk and valve case are contacting each
other.
Since this knocking noise leaves me feeling uncomfortable, and I suspect
that this is affecting the valve more than a little, are there any valves
that can deal with this problem?

|
According to our cause investigations...
|
The valve swings according to the increase and decrease in the flow amount,
and if the flow amount changes severely, the valve swings accordingly.
As a result, it slams against the valve case causing noise.
This is not just a noise problem, but also one that is affecting the valve
disk and valve case to the extent of causing damage.

|
How about the Non-Water Hammer Check Valve?
|
The valve disk has hard rubber for buffering (6) attached in the area where
it contacts the valve case, so this protects both the valve disk and valve
case when the valve is fully opened and pushed against to valve case, or
when it is in continuous contact according to the flow amount change.
According to our investigation, only our check valve handles this kind
of problem.
In this way, YOKOTA has the persistence to create products meticulously
by taking all details into consideration.
Construction and operation comparison table for various check valves
Classification
|
Immediate closure type
|
Slow closure type
|
YOKOTA Non-Water Hammer Check Valve
(PAT., Rapid closure type)
|
Counter-weight type
|
Coil spring type
|
Dashpot type
|
Construction
|
|
|
|
|
Operation
|
By effectively utilizing the shape of the valve disk and valve seat, the
check valve closes at the moment when the flow direction inside the pipe
changes from the normal to the reverse direction, with the flow speed at
zero after the pump stops. This is called the rapid closure type.
|
In order to keep up with the flow speed during the flow direction change,
an arm and weight is installed to the valve shaft, always applying force
in the valve closure direction, so that when the flow speed decreases,
the valve rapidly closes by the weight suppressing the valve disk.
|
In order to keep up with the flow speed during the flow direction change,
a coil spring is installed to the valve shaft, always applying force in
the valve closure direction, so that when the flow speed decreases, the
valve rapidly closes by the coil spring suppressing the valve disk.
|
After the flow direction inside the pipe is changed from the normal to
the reverse direction, the dashpot applies brakes from the outside so that
the valve does not close rapidly by the reversed flow, and closes gradually
resisting the reversed flow. This is called the slow closure type.
|
Wear caused by sludge, corrosion from seawater, and water hammer caused
by water column separation....The YOKOTA Non-Water Hammer Check Valve solves
these three difficult problems.
The YOKOTA Non-Water Hammer Check Valve (PAT.) features

|
Due to the valve response according to the water flow, there is no delay
in valve closure and water hammer does not occur.
|

|
The simple, single-disk construction eliminates breakdowns and maintenance
costs can be reduced considerably.
|

|
As safety equipment that prevents dry operation of pumps, the No-Feed Detector
can be equipped (option).
|
In addition, YOKOTA's Seawater Resistant Stainless Steel Casting YST130N
is available (option).
The YST130N is a duplex type stainless steel alloy, which has been developed
originally at YOKOTA, and it has extraordinary seawater and chemical resistance. |
Pressure change with time after
pump operation is stopped
|
YOKOTA Non-Water Hammer Check Valve
|
|
Conventional check valve
|
|
|
|
For details of each product, please refer to
Non-Water Hammer Check Valve SL series
Seawater Resistant Stainless Steel YST130N
|